Feature
Invisible PET Recycling Revolution: On Convenience Store Shelves and Beneath Our Feet
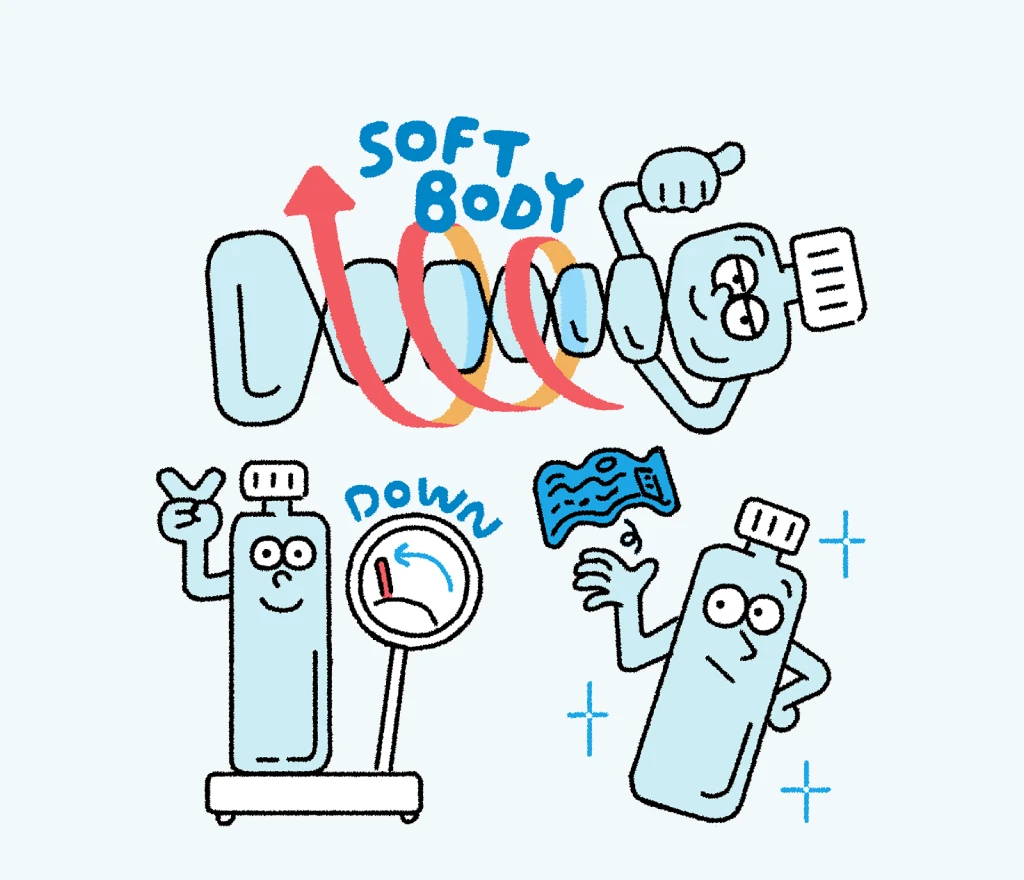
Index
Label-Free and Lightweight: The Evolving PET Bottle
How Many Times Can a PET Bottle Be Recycled?
HELIX: The Infinitely Recyclable PET Resin
New Trac: Bringing Hard-to-Recycle PET Materials Back into the Loop
Focusing on the ‘Invisible Revolution’ That Supports Our Lives
PET bottles are deeply embedded in our daily lives, so much so that there’s hardly a day we go without using one. Yet behind the scenes, significant changes are taking place. Revolutionary advancements in recycling technology are emerging.
With chemical recycling technology, recycled PET resin called “HELIX™” enables repeated recycling without degradation. Meanwhile, “New Trac” reinforces Japan's roads by recycling PET materials that are otherwise difficult to reuse.
Join us as we explore the fascinating forefront of PET recycling innovations.
Label-Free and Lightweight: The Evolving PET Bottle
PET (polyethylene terephthalate) is a petroleum-derived synthetic resin widely used in PET bottles, food packaging, clothing, and more. While PET bottles have become an essential part of our daily lives, have you ever wondered how many are distributed each day and how many of those are actually recycled?
According to data from the PET Bottle Recycling Promotion Council, approximately 630,000 tons of designated PET bottles were sold domestically in 2023. This is equivalent to roughly 31.5 billion 500ml PET bottles. Of these, around 540,000 tons were recycled. In other words, an impressive 85% of the vast number of PET bottles used are collected and recycled.
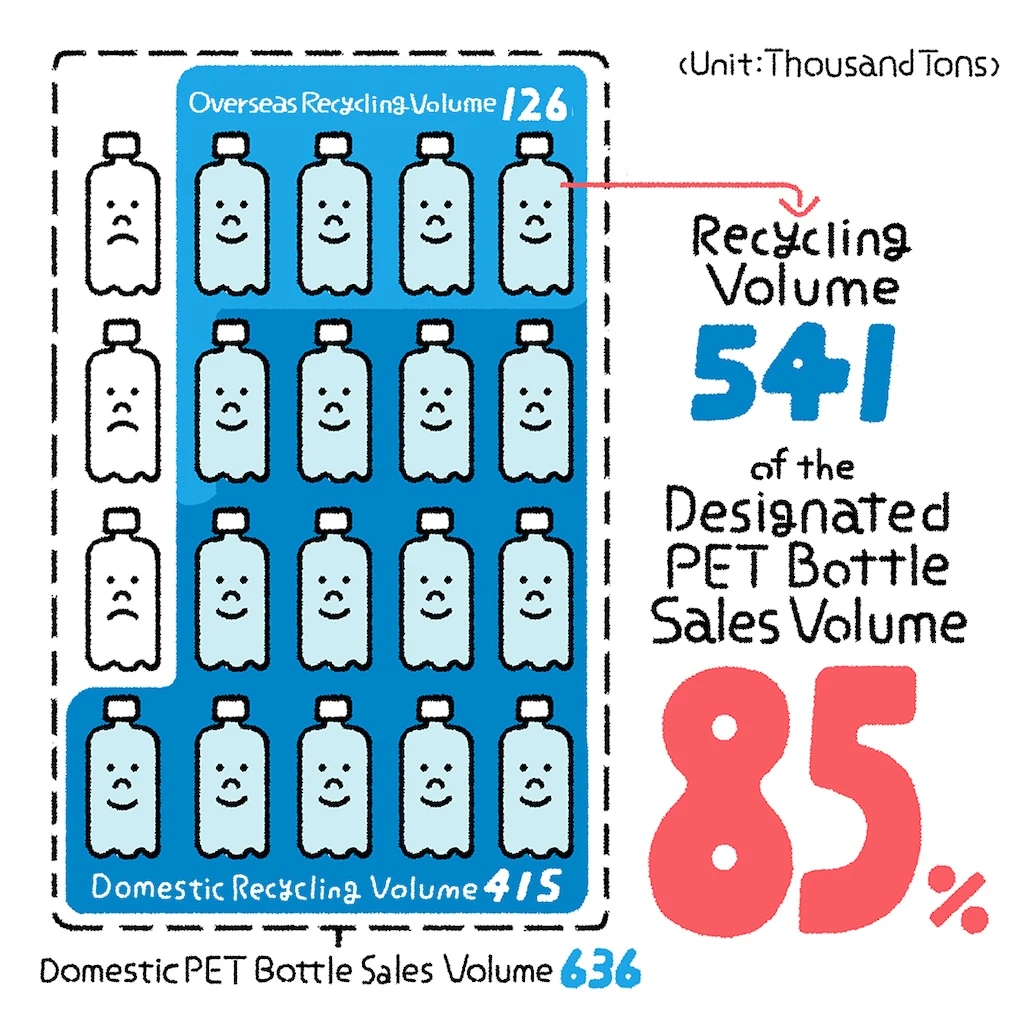
This recycling rate is remarkably high even when compared to Western countries. The key to achieving such a high recovery rate lies in the recycling infrastructure that has been developed since the 1990s. Various collection routes have been established, including municipal sorting systems, collection boxes at supermarkets, and bins placed beside vending machines.
Alongside these recycling initiatives, PET bottles themselves have continued to evolve. One prominent example is the increasing presence of “label-free bottles.” Not only do they eliminate the hassle of removing labels, but they also do away with the adhesives used on labels, allowing for higher-purity recycling.
Many people may have also noticed that PET bottles have become lighter in recent years. When PET bottles first became widely available in the 1990s, a 500ml bottle weighed approximately 40 grams. Today, that weight has been reduced to around 20 grams. This reduction conserves resources and contributes to lower CO₂ emissions during transportation. More recently, PET bottles have become softer and easier to crush, improving the efficiency of collection and transportation. This change has also streamlined the recycling process, making the material easier to handle during processing.
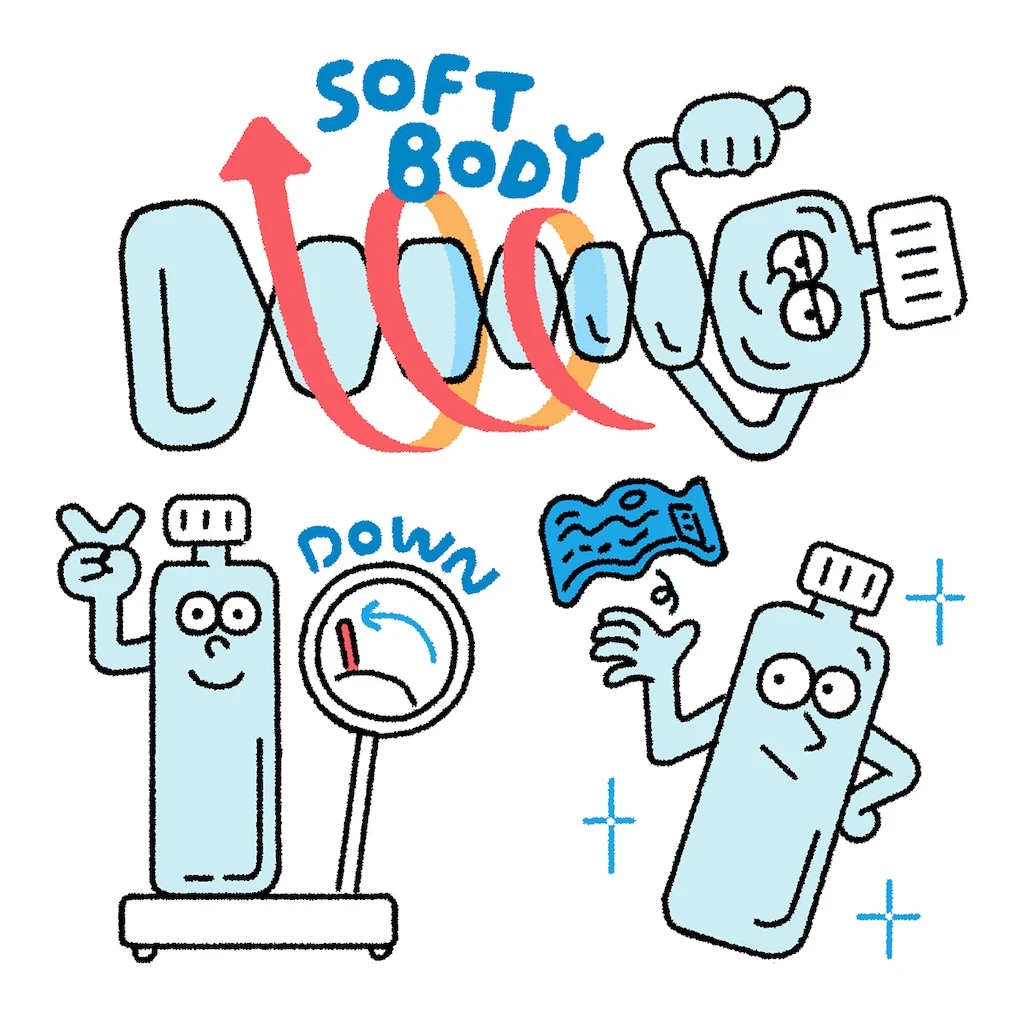
However, not all collected PET bottles are reborn as new PET bottles. The proportion of PET bottles recycled back into new bottles, a process known as “bottle-to-bottle” recycling, remains at around 30%. The primary reason for this is the presence of “impurities.” Even PET bottles that appear clean may contain tiny, invisible pigments or metals. Despite careful washing at home, it is difficult to completely remove these impurities. PET bottles with a high level of impurities significantly reduce the quality of recycled products, making it difficult to reuse the material multiple times.
How Many Times Can a PET Bottle Be Recycled?
Used PET bottles are generally recycled through two main methods: “material recycling” and “chemical recycling.”
Material recycling is the most common method currently used in Japan. In this process, PET bottles are finely crushed, melted down with heat, filtered to remove larger impurities, and then solidified back into resin. While this method can eliminate visible impurities, smaller contaminants such as pigments often remain.
Chemical recycling, on the other hand, breaks down PET at the molecular level to remove impurities. Plastics are composed of over ten thousand molecules (polymers) linked like a long chain. Chemical recycling cuts these chains through chemical reactions, breaking them down into smaller units called monomers. This process effectively removes impurities, leaving behind purified material that can be used to produce PET resin of the same quality as petroleum-derived PET. As a result, this method enables PET bottles to be recycled repeatedly without degradation.
However, chemical recycling is more costly compared to material recycling. To achieve successful “bottle-to-bottle” recycling, combining both material and chemical recycling methods is essential.
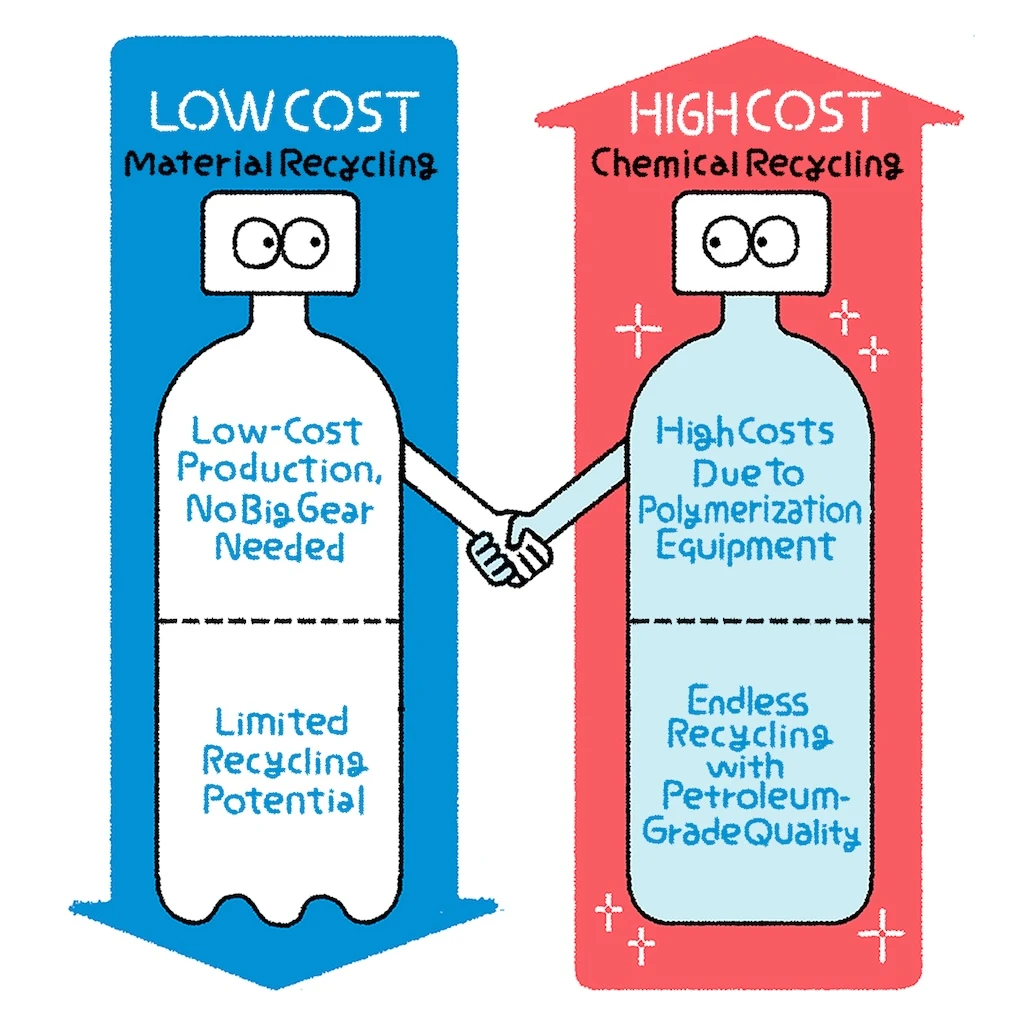
HELIX: The Infinitely Recyclable PET Resin
In 2024, PET Refine Technology Co., Ltd., the only company in Japan operating a commercial-scale chemical recycling plant, launched its brand of recycled PET resin called “HELIX.” The name “HELIX,” meaning “spiral” in English, symbolizes the company’s goal of achieving technology that allows PET bottles to be recycled repeatedly in a continuous loop.
The process of recycling used PET bottles into HELIX involves two main steps. The first step is breaking down the used PET bottles at the molecular level to remove impurities. The second step involves reconnecting the purified molecules to regenerate PET resin once again.
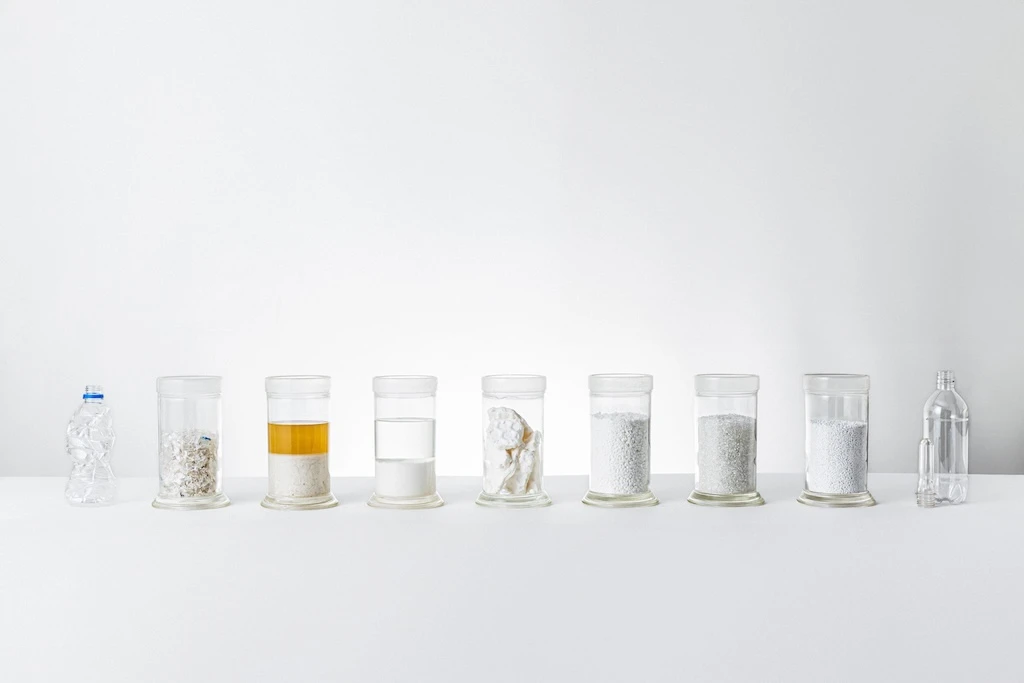
The greatest feature of the recycled PET resin produced through this process is its ability to maintain quality even after repeated recycling, thanks to the removal of impurities. Additionally, the production process for HELIX achieves a 47% reduction in CO₂ emissions compared to conventional petroleum-based production.
(For more details, visit JEPLAN Sustainability)
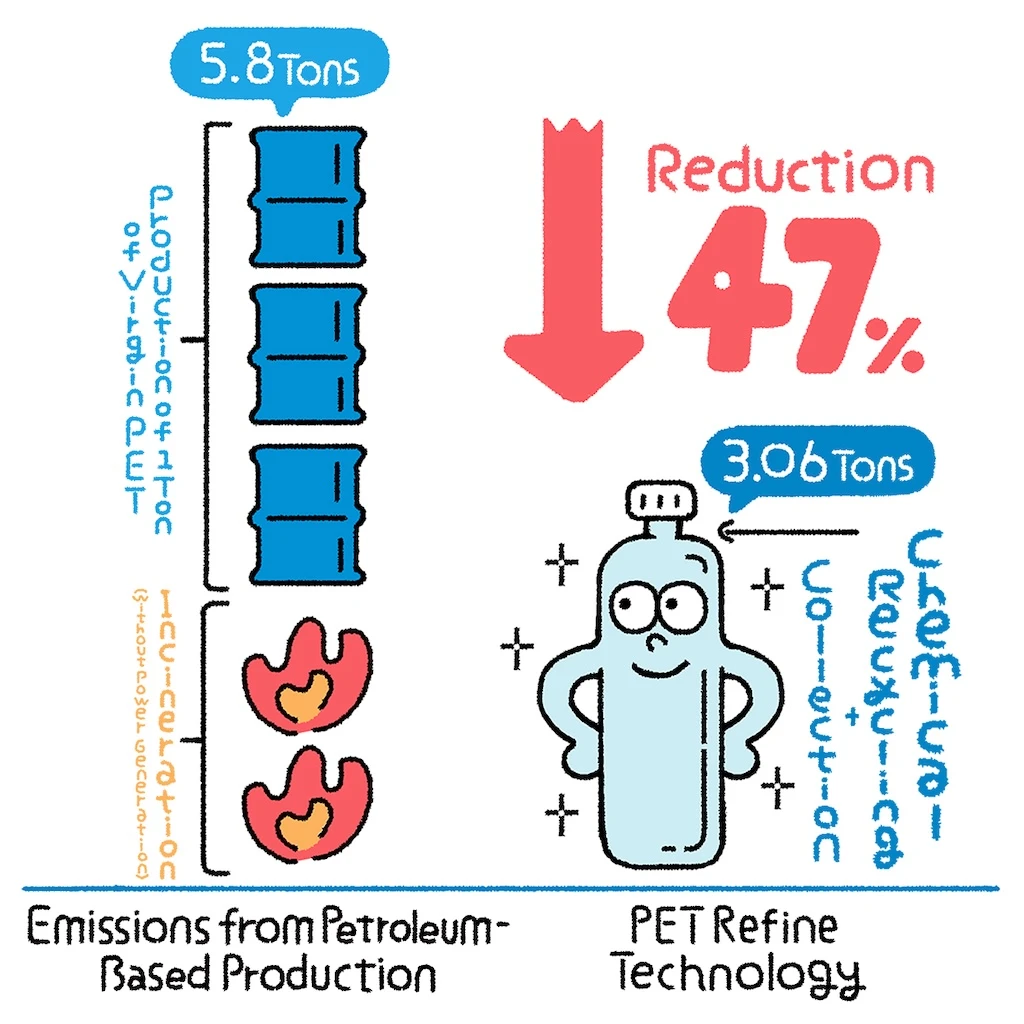
The foundation of this technology was established about 20 years ago. However, there were two major hurdles to overcome before operating a plant on a commercial scale.
The first challenge was mass production. While the technology worked on a small scale, scaling up PET resin production presented numerous technical difficulties. “There were times when the plant’s pipes would get clogged, forcing us to shut down the factory,” recalls Daigo Iga, President and CEO of the company, reflecting on the struggles faced during the early development phase.
The second hurdle was cost. Chemical recycling consumes significant energy during the production process, making it more expensive than conventional material recycling. Although the technology itself was feasible, ensuring economic sustainability proved to be a major obstacle.
A turning point came in 2018 when beverage manufacturers began setting ambitious targets to use “100% environmentally friendly materials by 2030.” As environmental concerns gained greater social attention, the value of chemical recycling was reevaluated. By forming partnerships with beverage manufacturers, who agreed to partially shoulder the costs, economic sustainability was achieved, accelerating the development and adoption of the technology.
As a result, chemical recycling now accounts for 10% of the total bottle-to-bottle recycling process, equivalent to 22,000 tons per year — roughly 1 billion 500ml PET bottles.
Today, HELIX is produced using 72% recycled PET bottles and 28% petroleum-derived materials. According to Iga, this is not due to technological limitations but rather a consideration of plant production efficiency. In fact, they have successfully produced 100% recycled products in the past and plan to gradually increase the proportion of recycled materials moving forward.
In the future, HELIX is expected to expand beyond PET bottles to a wider range of products, including cosmetic containers and industrial goods. The day when true “continuous recycling” becomes a reality may be just around the corner.
New Trac: Bringing Hard-to-Recycle PET Materials Back into the Loop
PET materials are used in many fields beyond beverage bottles. In everyday life, they are found in cosmetic containers and textile fibers, while in industrial applications, they are used as protective films for electrical and electronic components. Just like beverage PET bottles, these PET materials are also recycled, quietly supporting our daily lives in ways we may not notice. One notable example is their use as a material that strengthens roads.
In 2021, Kao developed an asphalt modifier called “New Trac,” which enhances the durability of asphalt pavement. This innovative product utilizes hard-to-recycle PET materials as its raw material, marking a significant breakthrough in recycling technology.
The raw materials used for New Trac include industrial films and PET fishing nets used in the fishing industry. Approximately 40% of New Trac's raw materials are recycled.
Industrial films are challenging to recycle due to their coatings and special treatments. Additionally, about 1,000 tons of fishing nets are discarded annually across Japan. These nets are often contaminated with salt or dyed black, making them unsuitable as raw materials for typical recycled products. As a result, they were previously disposed of through incineration or landfill. However, Kao found a new purpose for these difficult-to-recycle materials by utilizing them in asphalt modifiers.
Asphalt mixed with New Trac has proven to be significantly more durable than conventional pavement. Experimental results show that adding just 1% of New Trac to asphalt mixtures can increase durability by approximately five times compared to asphalt without the additive.
In Japan, 95% of roads are asphalt-paved. However, during the summer heat or under the weight of heavy vehicles, these roads are prone to deformation. Such deformation increases the risk of traffic accidents and requires frequent repairs. More frequent repairs lead to traffic congestion, which in turn raises CO₂ emissions.
By improving asphalt durability and promoting PET material recycling, New Trac addresses both challenges simultaneously, contributing to environmental impact reduction. Notably, New Trac will also be used at the site of Expo 2025 Osaka, Kansai. This initiative offers a meaningful opportunity for people to recognize how PET materials, though invisible to the eye, continue to support our everyday lives.
Focusing on the ‘Invisible Revolution’ That Supports Our Lives
PET Refine Technology has developed a groundbreaking method that breaks down and regenerates PET at the molecular level, completely removing impurities that could not be eliminated through conventional methods. This enables PET bottles to be reborn repeatedly with no loss in quality. Meanwhile, Kao has pioneered a new form of resource circulation by repurposing previously hard-to-recycle materials such as fishing nets and industrial films into road paving materials.
However, the efforts of both companies go beyond technological innovation. Achieving sustainable resource circulation requires building a system that involves society as a whole. PET Refine Technology collaborates with over 40 municipalities across Japan to promote the circular use of PET bottles collected from local communities. Kao has set an ambitious goal of achieving “waste negative” status by 2050 — meaning the company aims to contribute to recycling more plastic than it generates through its own packaging. By driving initiatives at the industry level, Kao is taking significant steps toward a more sustainable future.
Yet, these efforts alone are not enough. The active participation and mindful actions of each one of us are crucial to making these goals a reality. The PET bottles we use daily, the roads we walk on — we may rarely give them a second thought. But behind the scenes, an “invisible revolution” is taking place, steadily pushing society forward.

Daigo Iga
Born in 1977 in Kumamoto Prefecture. In 2010, Iga joined Japan Environment Planning Co., Ltd. (now JEPLAN, Inc.). He was involved in the launch and operation of a bioethanol production plant that utilized cotton fiber. In 2017, he played a key role in establishing the Kitakyushu Hibikinada Plant, where he served as the plant manager, overseeing operations that produced recycled PET resin from collected clothing. In 2020, Iga was appointed President of PET Refine Technology Co., Ltd., a JEPLAN Group company. In this role, he has been promoting the “bottle-to-bottle” initiative, which produces new PET bottle raw materials from used PET bottles using chemical recycling technology.
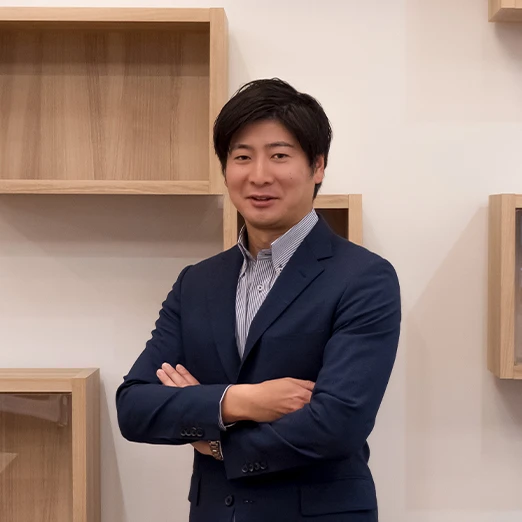
Akihiro Nagasawa
During his university years, Nagasawa studied abroad in Brazil as part of his soccer experience. Embracing the motto of “competing on a global stage,” he has been actively involved in expanding Kao's chemical business worldwide since joining the company. Drawing on five years of experience working in the United States, he now leads the global expansion of Kao's asphalt business, working closely with his team to drive progress forward.
Photo courtesy of: PET Refine Technology Co., Ltd. / Kao Corporation