- Locale
- ja
- en
Feature
What is the Green Innovation (GI) Fund? – Part 2 A New and Unknown Future Taking Shape! Opening the Doors of Imagination Through the GI Fund
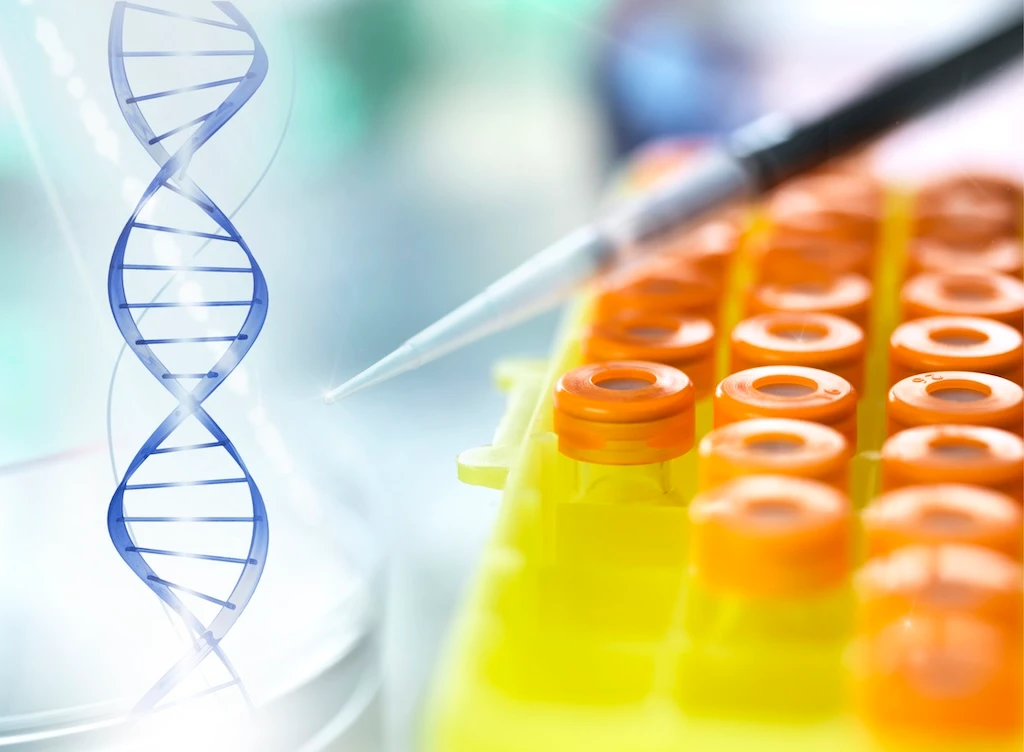
The Green Innovation (GI) Fund was established by the Japanese government to support companies in becoming carbon neutral. Since the fund's establishment in 2020, a number of corporate projects have been selected, and new technologies and research results that will transform society are taking shape. Today we spoke with companies and organizations taking part in the exhibition at the Japan Pavilion that are also promoting GI Fund projects, to hear about the exciting future they envision.
Utilizing “CO₂-eating Microorganisms” Across the World of Biomanufacturing
─ National Institute of Technology and Evaluation (NITE)
There are many microorganisms in our world that benefit human life and health. The National Institute of Technology and Evaluation (NITE) preserves microorganisms and provides them alongside relevant information to companies and research institutes. Among many microorganisms, CO₂-fixing microorganisms have unique characteristics. While ordinary microorganisms consume organic substances and decompose them to produce various substances, CO₂-fixing microorganisms consume CO₂, an inorganic substance, and produce usable organic substances. Dr. Mori of NITE, who has been studying microorganisms for over 20 years, states, “Atmospheric CO₂ is a ‘vilified molecule’ that is increasingly prevalent worldwide. But if CO₂-fixing microorganisms that consume atmospheric CO₂ were utilized in manufacturing across industries, it could truly transform society.”
Mori continues, “Looking ahead, we need to gradually increase the products around us that use chemicals produced by microorganisms from CO₂. Yet currently, many microorganism-derived products are expensive, making it unlikely they will be used in our daily lives anytime soon. They are expensive because development, improvement and cultivation of microorganisms is extremely challenging and requires specialized techniques that are costly. Only a few companies with the necessary knowledge and technology can handle them, and manufacturing with microorganisms is a major challenge.”
To make microbial-based manufacturing accessible to all companies, NITE has started developing a platform where researchers aiming to create products from CO₂ can access information on CO₂-fixing microorganisms.
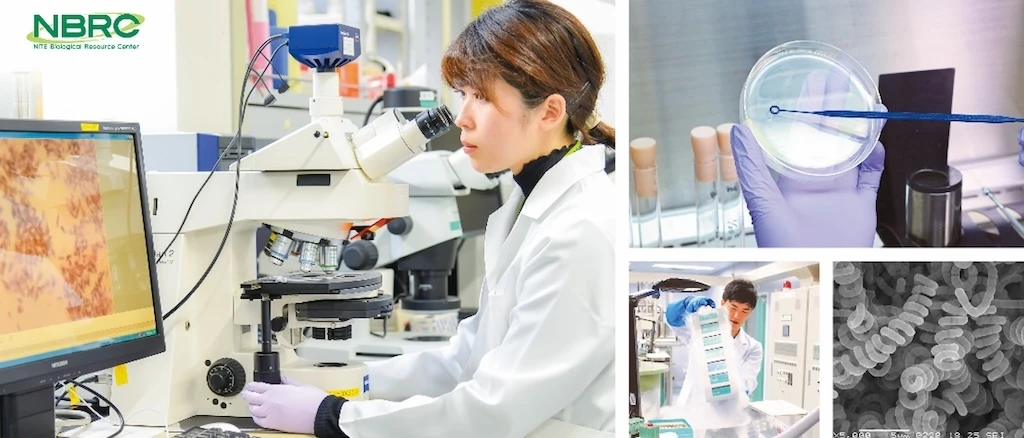
The platform functions like a search engine. Once it is up and running, if company researchers want to make polymers using a particular microorganism, they will be able to search for related microbial species, necessary genomic editing information, cultivation methods and more, and apply this information to their own manufacturing.
The goal is to create a foundation for microorganism utilization that anyone can access without specialized knowledge or skills, a place where people can find valuable information on utilizing microorganisms. This proposal was adopted by the GI Fund, leading to a more extensive search for CO₂-fixing microorganisms and expansion of related information, according to Mori.
Mori also details, “Compared to conventional petroleum-based resources, there is still room for improvement in terms of cost, quantity and performance of the organic matter produced by CO₂-fixing microorganisms. That’s why collaboration is essential – companies that excel in plant construction, cultivation techniques and other specialized areas need to work together, rather than each company manufacturing products in isolation.”
He continues, “I truly hope that this platform will function as a bridge between research institutions and companies, and accelerate the societal application of microorganisms. I've been studying microorganisms for a long time, and they have incredible potential. I sense we will develop further utilization methods for microorganisms and discover other amazing powers they have moving forward. I hope that the younger generation will take an interest in microorganism research and join us in furthering R&D in the field.”
Check it out!
In the Farm Area of the Japan Pavilion, the “Transformation Relay” exhibit showcases how organic waste is decomposed by microorganisms, producing substances and energy that are then transformed by other microorganisms. Here, five BE@RBRICK designer toys generated from waste choose their own path and continue on a unique journey. Fireworks will illuminate the moment BE@RBRICK encounters microorganisms in action, offering visitors a spectacle of transformation. The BE@RBRICK toys will become as one with the microorganisms, transforming into new materials and embarking toward the colorful future that awaits them. The exhibit is based on information regarding microorganisms that NITE has accumulated through extensive research over the years.
Creating Plastic Materials From CO₂ Emitted by Waste Incineration Plants?
─ SEKISUI CHEMICAL CO., LTD.
Many different industrial products – home appliances like TVs, electronics such as smartphones and computers, as well as vehicles such as airplanes and cars – rely on specialized adhesives to bond components. These adhesives require a high level of functionality, such as resistance to sudden changes in air pressure and temperature for airplanes, and they must not affect the performance of electronic devices such as smartphones and computers.
SEKISUI CHEMICAL, a major manufacturer of these high-performance plastics, faced the challenge of creating a cycle of resource use. Dr. Ono in charge of technology development at SEKISUI CHEMICAL explains, “High-performance plastics are made from a complex combination of monomers, additives and materials, rather than a single monomer. Products made from a single monomer, like plastic bottles, can be recycled back to the raw material state, but products created from a mixture of monomers cannot be easily broken down into their constituent materials, so they have to be disposed of through incineration. We have been tackling social issues since the end of World War II, and contributing to environmental solutions has been a major concern for us.”
Around 2010, SEKISUI CHEMICAL began researching whether they could make high-performance plastics from the CO₂ generated by incineration. While examining an array of global technologies, they discovered there were microorganisms that consumed CO₂ and other gases and produced ethanol. Upon verification, it became clear that it was indeed possible to produce organic compounds from gases. However, there was a major hurdle to producing high-performance plastics from microorganisms – the gasses contained components that inhibited the reactions of the microorganisms.
“We applied a proposal to the GI Fund along with research institutes specializing in microorganisms. Our proposal was accepted, and we began developing a microorganism that could produce the desired chemicals. It was difficult to increase functionality while reducing inhibition against their growth, because of the constantly changing chemical composition of syngas. From this emerged the ‘CO-assimilating bacteria’ that consume carbon monoxide (CO) and produce monomers for highly functional plastics,” explains Dr. Ono.
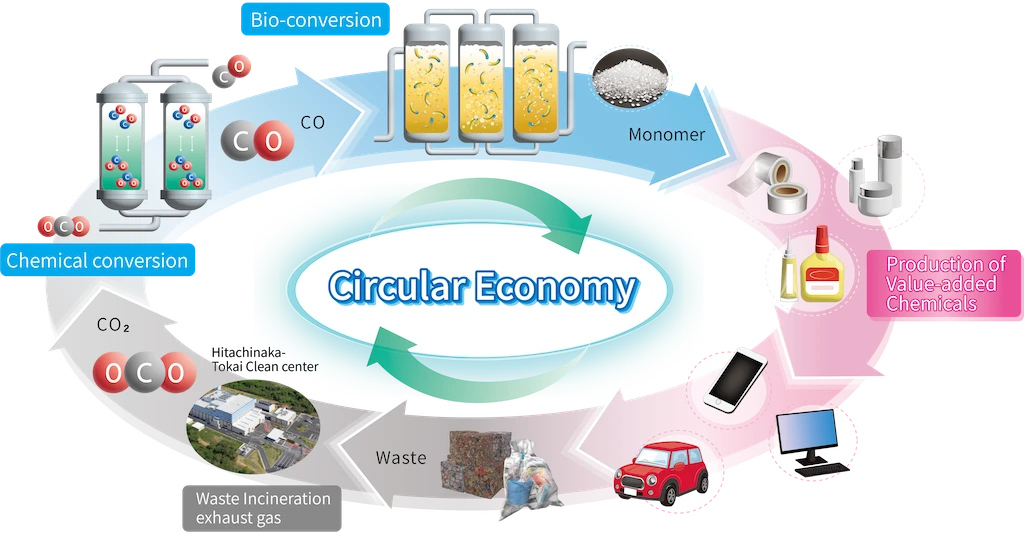
SEKISUI CHEMICAL's expertise as a chemical manufacturer is leveraged in the technology for converting CO₂ to CO and in the construction of microorganism cultivation systems. The advanced technologies that have developed over the years are also utilized to manufacture highly functional plastics from polymer precursors.
“We are not just reducing CO₂ but utilizing it as a resource. If this initiative, which is taking shape through the GI Fund, is socially implemented, the ‘waste’ we produce will become part of the production cycle and hence an important resource. The challenge of making plastics again from CO₂, which initially seemed unlikely to succeed, is finally taking shape. We want to contribute to creating infrastructure and environments where people can live with peace of mind,” details Dr. Ono.
Check it out!
In the Farm Area of the Japan Pavilion, the “Transformation Relay” exhibit showcases how substances and energy such as water, heat, electricity, CO₂ and nutrients from the Plant Area can be transformed into new forms by microorganisms. One type of these microorganisms is SEKISUI CHEMICAL's “CO-assimilating bacteria,” a new technology to curb CO₂ emissions and help realize a carbon-neutral society by converting CO₂ into a resource.
Creation and Decomposition by Microorganisms: Creating a “Cycle” with Biodegradable Plastics
─ Kaneka Corporation
In the 1960s, research into producing proteins from inexpensive petroleum-derived hydrocarbons was booming, and Kaneka Corporation (hereafter “Kaneka”) was one company working on this technology. Although the research did not lead to practical applications, “hydrogen-oxidizing bacteria” attracted attention during that period as microorganisms that could produce high-quality proteins from CO₂ rather than from petroleum. At the time, biodegradable polymers produced by hydrogen-oxidizing bacteria were regarded as an obstacle to protein production, and research was even carried out to determine how to prevent the polymer formation.
Kaneka began developing biodegradable plastics in the 1990s. At the time, plastic waste ended up in a landfill rather than being incinerated, and this led to a shortage of landfill sites alongside soil contamination. The company's researchers wondered if there were any plastics that could be decomposed by microorganisms even when buried underground, and continued their search for new microorganisms.
As luck would have it, they discovered a microorganism in the soil at one of Kaneka's factories that produced a new polymer with the potential to replace existing plastics! However, the microorganism was not strong enough to store biodegradable polymers, so they combined it with hydrogen-oxidizing bacteria that could. In this way, they succeeded in producing a polymer that can be used in plastic products through the power of hydrogen-oxidizing bacteria. This polymer is a precursor for biodegradable plastics, and Kaneka began production at a large-scale facility in 2011.
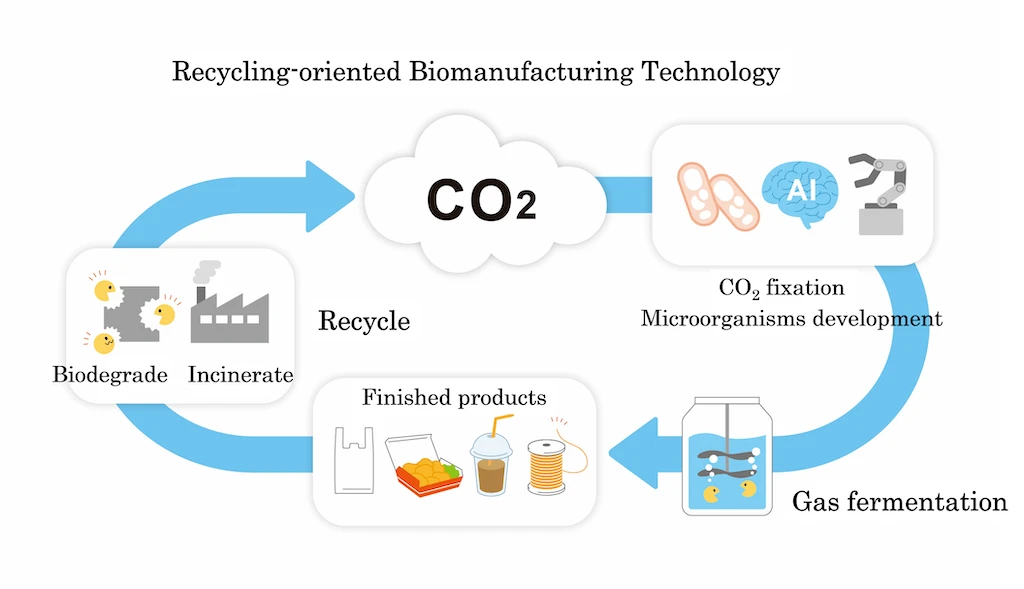
Mr. Sato, head of the CO2 Innovation Laboratory, explains, “The biodegradable plastics currently on the market are made by using vegetable oil or used cooking oil to produce polymers. However, given the challenges inherent in ensuring a stable supply of vegetable oils and the issue of global warming caused by CO₂, we have set our sights on polymer production using CO₂ as a precursor. With the support of the GI Fund, in 2023 we started research on microorganisms that produce biodegradable plastics directly from CO₂ as well as the development of a related manufacturing process.”
Through trial and error, Kaneka is aiming to scale up from the lab to the factory, which will involve creating a factory that can safely handle the three gases used as raw materials – CO₂, hydrogen and oxygen – and managing their concentrations to ensure that the hydrogen-oxidizing bacteria are active and producing large quantities of polymers.
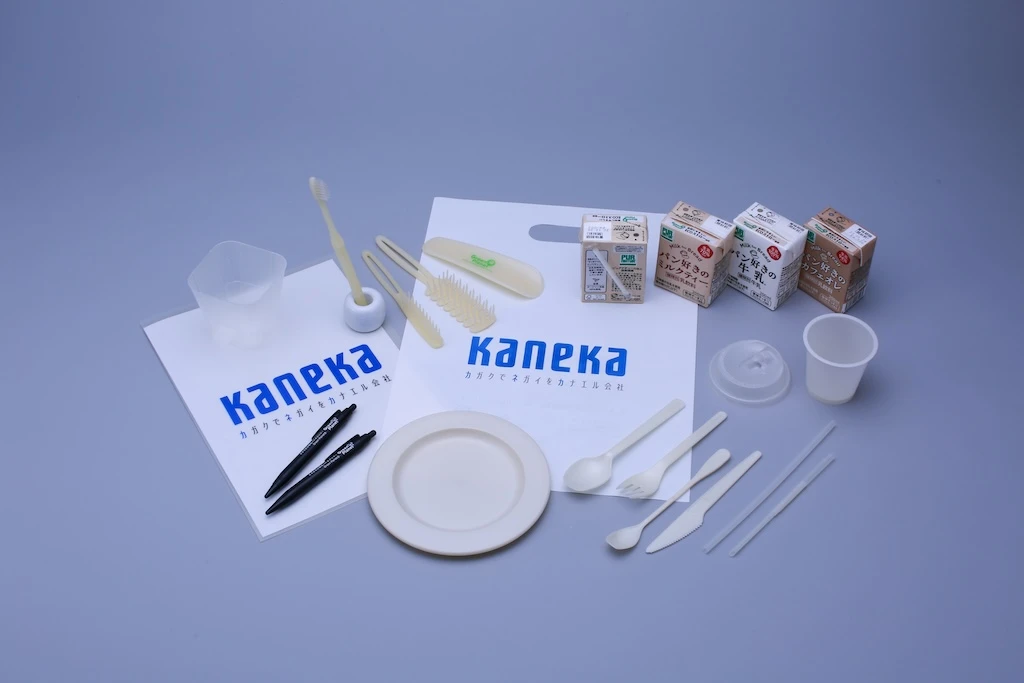
Biodegradable plastics are already used in everyday products, such as hotel amenities and café straws. “People may not notice these plastics being used, but that's exactly what makes them so great: they blend in seamlessly. Producing straws and cutlery from biodegradable plastics requires rethinking everything from molding techniques to machine operating conditions from scratch. While conventional molding technologies using polyethylene and polypropylene have become so established that almost no one is attempting to develop or improve them any further, Kaneka has chosen to use a proprietary molding process that is the most complex in the world. Moving forward, we need to expand the range of products we can make from microorganism-derived materials. I would like to create an even greater ‘cycle’ by getting many people interested in how to utilize what microorganisms can produce for human society, and by continuing to share knowledge, technology and ideas,” details Sato.
Check it out!
In the Farm Area of the Japan Pavilion, the exhibit “What Can We Make With CO₂?” features a line of cylinders that are ferried out from a tunnel. The cylinders, which are filled with CO₂ derived from food waste, are met by vessels made of biodegradable plastic, themselves created from CO2. And in the Plant Area “The Boundless Potential of Microorganisms” exhibit, visitors can witness the process of identically shaped biodegradable plastic vessels gradually losing their original appearance as they are decomposed by microorganisms in an aquarium.
Absorbing CO₂ and Creating Products: The Power of Algae to Change the World!
─ Chitose Laboratory Corp.
Microorganisms play a vital role in producing essential items, from food seasonings to pharmaceuticals that support human health. Chitose Laboratory Corporation (hereafter “CHITOSE”) brings out the full potential of microorganisms and cells to deliver meaningful technology to different companies and in diverse research settings. With expertise in strain development, improvement and efficient cultivation methods, CHITOSE is extremely well-versed in the field of microbial technology. CHITOSE focuses on the potential of algae, a type of microorganism as described above. But why algae? The reason lies in their capacity for photosynthesis.
Dr. Fujita, Founder & CEO of CHITOSE Group, offers insight: “The resources we use today are organic matter produced by algae and plants through photosynthesis long ago, fossilized in the ground over vast periods of time. We use these organic materials by converting them into energy through combustion, respiration, fermentation and other oxidative processes. What we are left with is CO₂, which accumulates without being converted into anything. Could we reuse CO₂ as an energy source by ‘reducing’ it back to organic matter? This was the starting point of our research – if the amount of energy derived from oxidation and reduction is the same, energy and environmental crises could be solved. Photosynthesis is the only technology that can be used for this kind of reduction.”
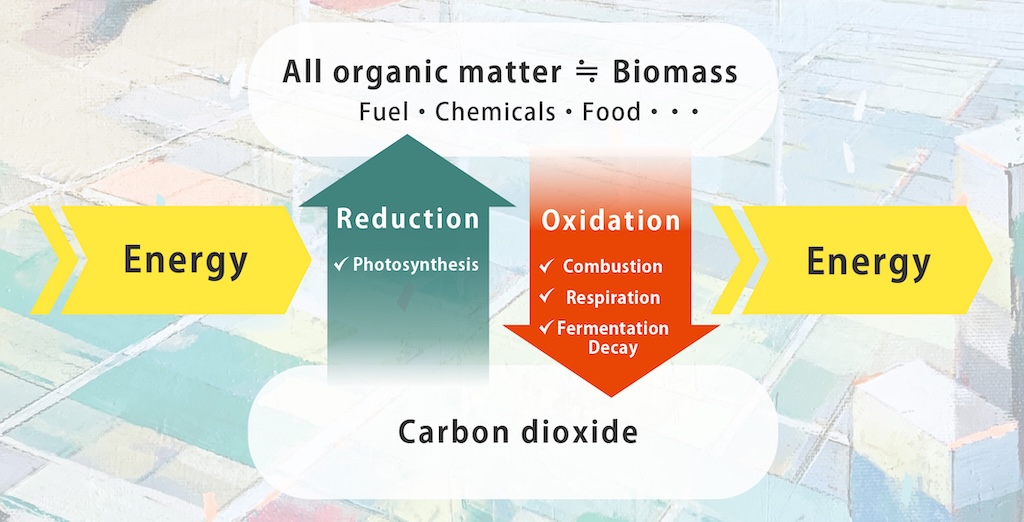
“Algae are one of the most powerful photosynthesizing organisms,” says Dr. Fujita. Compared to corn, soybeans and palms, algae are extremely efficient in producing oil through photosynthesis, and have significantly higher protein production rates. Algae also require very little water for photosynthesis, and as a result can produce organic matter even in deserts and salt-affected areas generally unsuitable for cultivation. Around 2010, CHITOSE started manufacturing products using algae by combining the two technologies of “strain improvement” and “mass cultivation” of microorganisms, which the company has been involved in for many years.
While developing algae technology in the laboratory, they also researched cultivation methods. After conducting lab-scale tests and production demonstrations, the company began operating a 5-hectare production facility in 2023.
Dr. Fujita explains further: “However, considering energy balance and environmental impact, we needed at least 2,000 hectares. That's why we decided to expand our operations with the support of the GI Fund. By 2027, we aim to be operating a 100-hectare plant capable of absorbing 14,000 tons of CO₂ annually, and by 2030, a 2,000-hectare plant absorbing 280,000 tons of CO₂ annually. By 2050, we plan to operate 10 million hectares, approximately equivalent to 1/20 of the global corn production area(*1). We estimate that this will allow us to produce twice the global protein demand(*2), for example, and at the same time absorb about 1/4 of Japan's annual CO₂ emissions.”
*1 The global corn cultivation area is approx. 190 million hectares.
*2 Assuming a daily protein requirement of 65 g per capita and a global population of 7.8 billion.
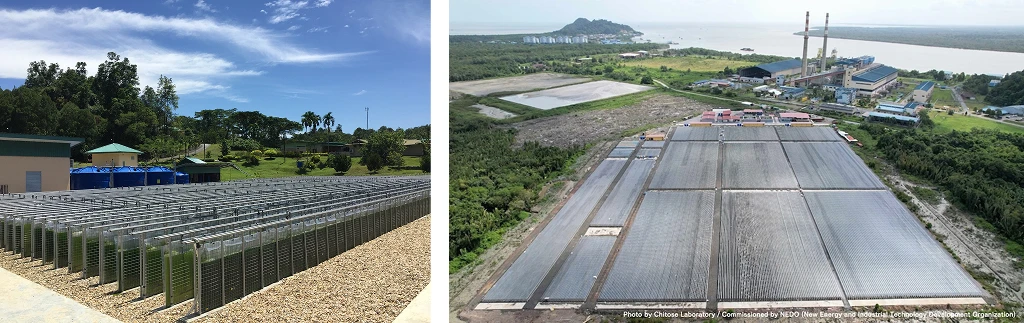
Algae produce different organic materials that can be transformed into jet fuel and foodstuffs, a few examples of how algae are expected to benefit our lives moving forward. CHITOSE has launched the MATSURI Project in collaboration with various companies and organizations to create an algae-based society. This project supports manufacturing in diverse fields including cosmetics, detergents, pharmaceuticals, supplements, sweeteners and food. If this initiative, accelerated by the GI Fund, becomes the norm, it will signify a significant step toward a future society where everyone can live fulfilling lives.
Check it out!
In the Farm Area of the Japan Pavilion, there are people taking care of an aquarium that doesn’t have any animals inside! The exhibit is called “Who Lives in This Aquarium?” and it's home to Botryococcus, a microalgae species currently cultivated by CHITOSE to produce oil similar to petroleum. Within the aquarium, the water ripples and shimmers, and tiny bubbles rise to the surface and disappear. The surface of the water reflects various colors in the spectrum of light, and one can sense the growth of microalgae. Though each individual alga is invisible to the naked eye, they can be experienced in this exhibit as a unified life form. Additionally, the “Curtain of Vibrant Algae Life” exhibit showcases the cultivation of Spirulina, a highly protein-rich algae that is also cultivated by CHITOSE. Visitors can observe it photosynthesize as it spreads throughout the space. Here, visitors can stroll through an otherworldly environment, woven out of green tubes, as if delving deep into a forest.
In the Japan Pavilion, visitors can see and feel the “seeds” of the future taking shape in a variety of areas, based on the theme of “circulation.” Visitors can also experience new technologies and research results that will create new forms of circulation in years to come. Perhaps here, you too will discover the power and ideas to create something that doesn't yet exist in our world.
Interviews supported by the National Institute of Technology and Evaluation (NITE), Sekisui Chemical, Kaneka Corporation / CHITOSE Laboratory Corporation
Text: Yukiko Oki
Let’s Share!
Do you want to be a part of “JUNKAN”?
Share your Japan Pavilion,
and ’circulate’ your thoughts.